As described in the genesis of this project, we apply our 50 years of experience to all our products. The production process usually starts with a request from one of our customers. In classic Abarth motorsport, original parts are very scarce and more fragile due to the old manufacturing techniques of the time. Therefore, most of the products in our catalogue are modelled after old originals that may have been damaged or where there was a demand for a stronger alternative.
Technical Drawing
When the request for a new part is finalized, we start to draw it up. Precision is paramount in this profession, no matter what. That is why every small rounding, indentation, slit or increase has to be written down to the millimetre. The more precise, the better the end result. This is a time-consuming step for good reason. It is also important that when drawing and measuring, a margin for handmade revision in the last step is taken into account.
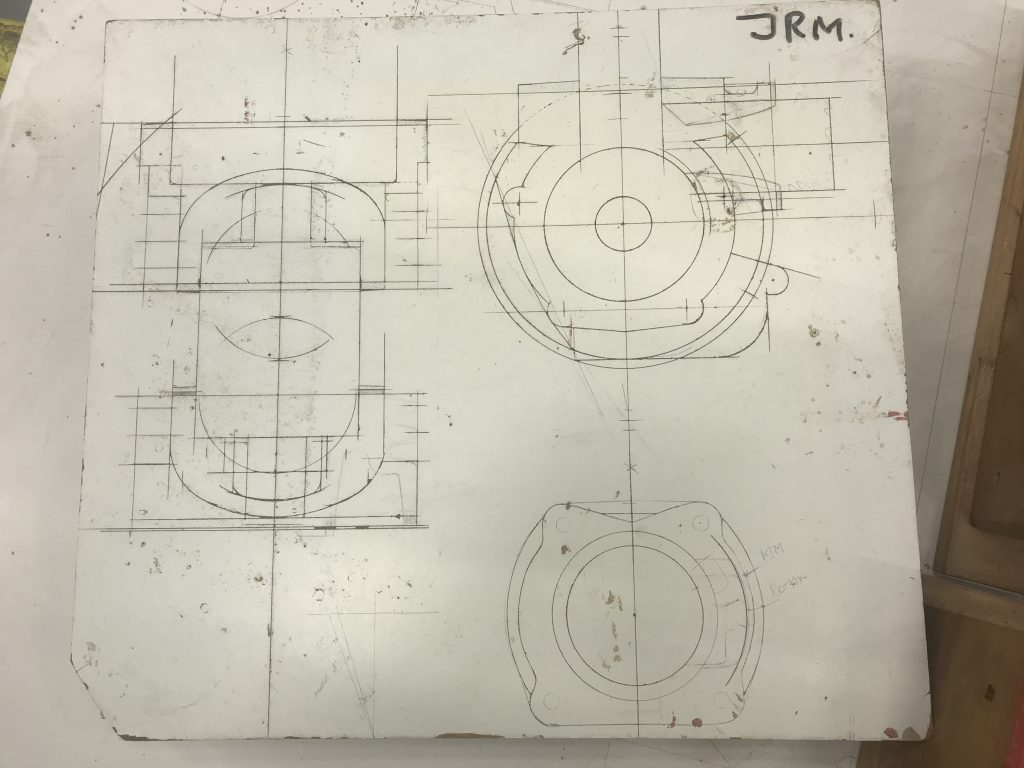
Constructing a model
This drawing is then used to make the actual model. This can be done in plastic, but in our case, wood is chosen more often. This model represents an inside-out (or inverted) version of the final product. With this model, a start can be made with the actual construction of the mould.
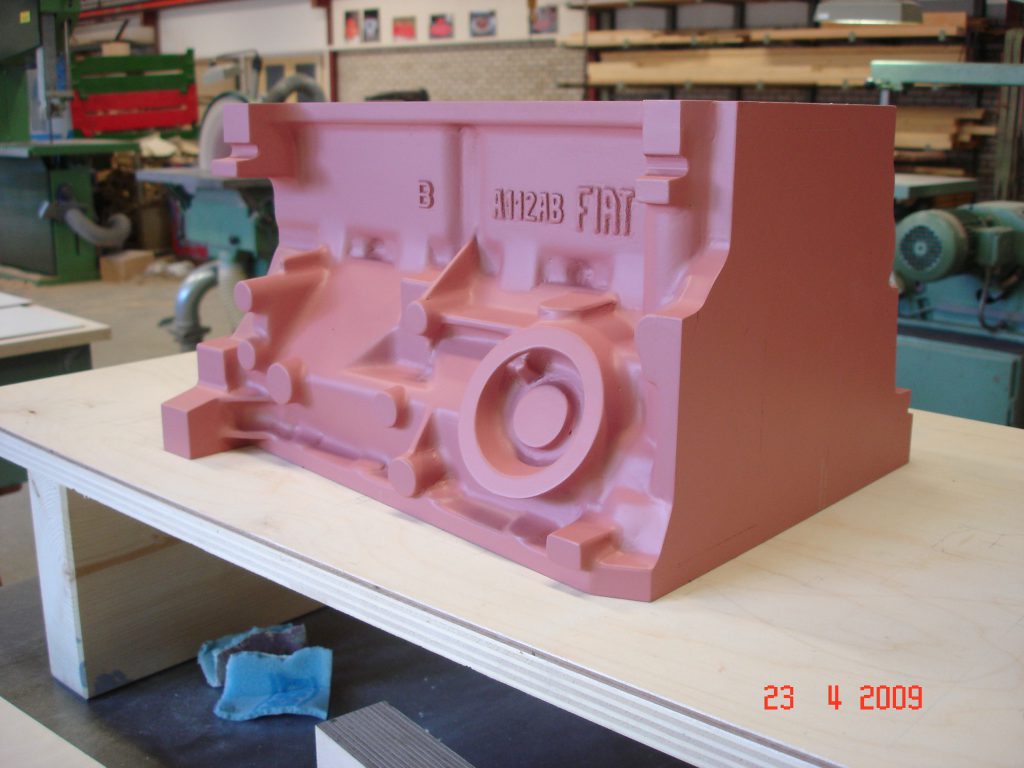
Building a Mould
When constructing the mould, we press the model into two sandboxes, so that two halves are created. When the mould is ready to be sent to the foundry, it must of course be possible to open it again by separating the two halves. With the sand print ready, the final step is underway. Both prints are filled with liquid aluminium, which is then given time to harden.
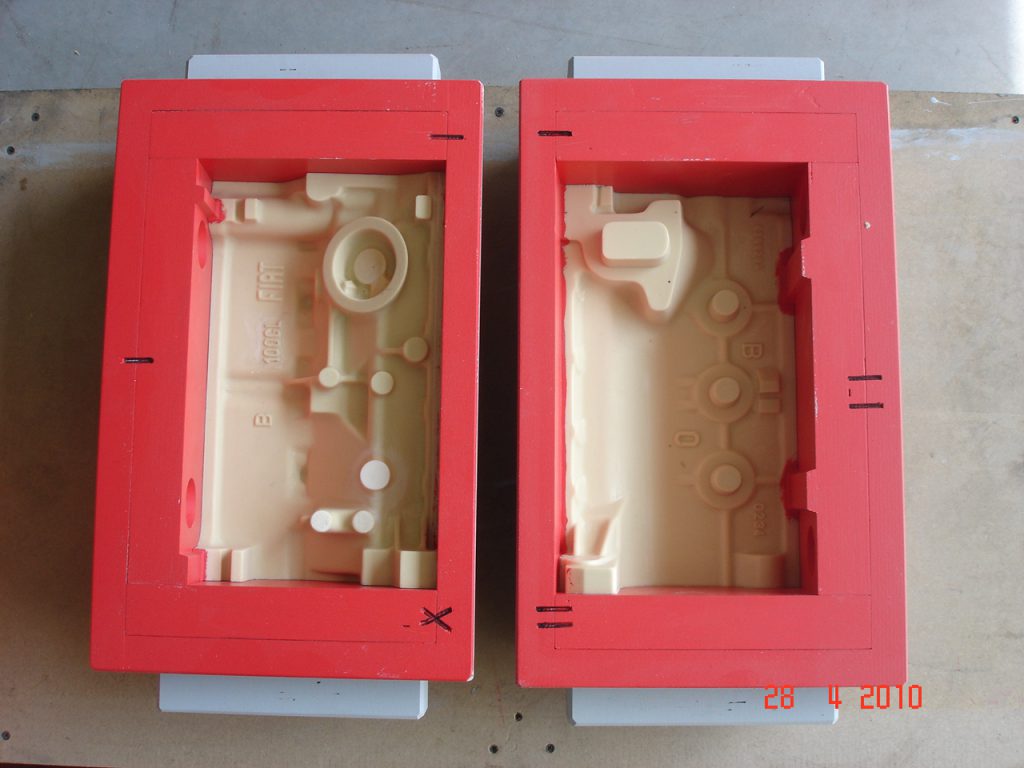
Finishing Touches
With the mould ready, it can go to the foundry to actually cast the product. Finally, we do the last finishing touches in house to achieve a professional result. This includes, for example, removing excess material and possibly giving parts a lick of paint.
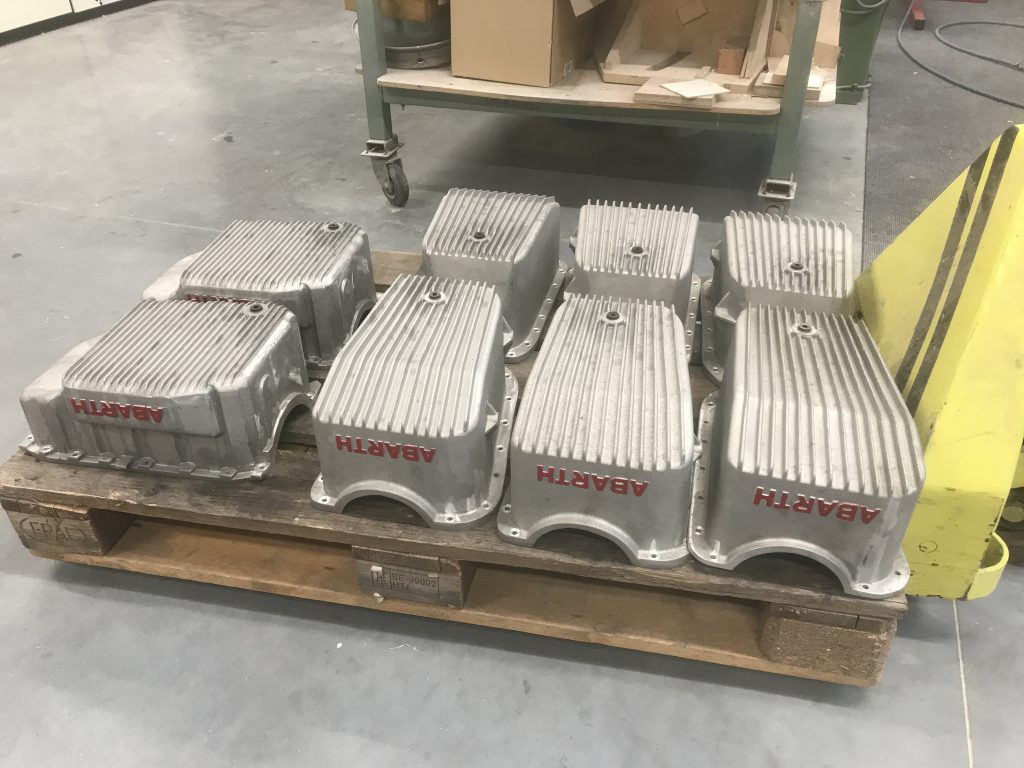